How Kanjivaram Sarees Are Made
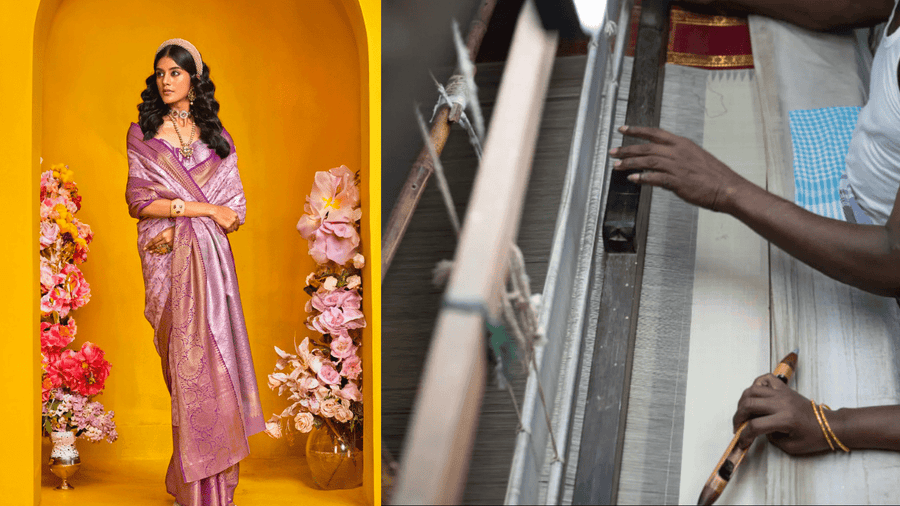
Kanchipuram (City of Thousand Temples) is located near Chennai in Tamil Nadu. This town has been famous for its silk weaving for centuries.
The earliest silk weavers were brought in during the reign of Raja Raja Chola I. Some People believe that these silk weavers were the descendants of Sage Markanda ( Celestial weaver of gods).

The Silk weaving craft in Kanchipuram is not written down or formally taught. It is handed over from one generation to the next. In most households, the loom sits beside the prayer space, and weaving is part of the family's daily rhythm.
How Kanjivaram Sarees Are Made

Unlike most silk sarees that are about 45 inches wide, Kanjivaram sarees are generally 48 inches wide. This gives them a broader drape. Each thread in a kanjeevaram saree is made using double warp, which means three silk threads are twisted together to form one strand. The warp frame holds around 60 holes in 1.2 inches. Through these, about 240 threads run. On the weft side, 250 to 300 threads are woven through. This dense build gives the saree its heaviness and durability.
A single kanjivaram saree may weigh between 500 grams and 1 kilogram, depending on its design and zari content.
The Silk
Only pure mulberry silk is used in making a kanjeevaram saree, and the silk is mainly sourced from Karnataka. The mulberry silk is first washed to remove any rubbles. It is then boiled in dye. The yarn is stirred gently while in the dye bath to ensure the colour spreads evenly. After this, it is washed again and left to dry in the shade. The yarn is then starched. This gives it strength and a faint sheen.
There are no cuts, joins, or mixed threads in genuine Kanjivaram silk.
The Border, Body, and Pallu of Kanjivaram Saree

In a Kanjeevaram saree, The Border, Body, and Pallu are woven separately. They are later joined by hand using a method known as korvai. This method is what allows Kanjivaram sarees to have contrasting body and border colours. The pallu is attached using a separate technique called petni. Unlike powerloom sarees where the design flows continuously, here, the parts are joined with care. This gives the saree strength and a distinctive finish.

Zari Work
Zari in a Kanjivaram sari is made using silver coated with gold. Traditionally, 1 Kg of zari used to include about 500 grams of silver and nearly 5 to 5.5 grams of gold. Today, most zari comes from Surat, Gujarat. However, the zari is tested at special centres in Kanchipuram to confirm its purity. The zari is usually twisted with silk thread and woven along with the fabric, not added separately.
Zari adds weight and value to kanjeevaram saree.
Motifs and Visual Identity

The motifs in a kanjivaram saree are drawn from Indian temple sculptures, natural elements, and daily life in South India. Some of the well-known Motif patterns include:
- Rudraksham: resembling sacred Rudraksha beads
- Gopuram: inspired by temple towers
- Mayilkan: the eye of the peacock
- Kuyilkan: the eye of the nightingale
- Mango, lotus, parrots, leaves, and checks
Some pallu designs in kanchi Pattu saree even depict episodes from the Mahabharata or Ramayana. In rare kanjivaram pieces, entire paintings are recreated in the weave.
The motifs in a kanjivaram saree are not surface decorations. They are built into the structure of the saree.

Time and Effort
It takes 10 to 12 days to weave a simple Kanjivaram saree. Bridal kanjivarams take up to 20 days. The work involved in making this saree is usually shared. One person manages the loom while the other prepares the thread or guides the shuttle. In many homes, the weaver and his wife work together. Even children take part by helping with winding or starching.
Kanjivaram Saree Finishing Process
After weaving, the saree is checked by eye and hand. Loose threads are trimmed. Any Minor mistakes are corrected. The silk saree is then folded with care. Many families place neem leaves or turmeric pieces with the kanjeevaram saree to protect it. Some wrap it in muslin or cotton before storage.
The Kanchipuram sarees are not hung like regular clothes. These sarees are laid flat and kept away from light.
GI Tag and Standards
Kanjivaram sarees are protected under India’s Geographical Indication (GI) Act. This means that to be called a Kanjivaram, a saree must be woven in the Kanchipuram district and follow precise rules.
According to the GI label, the zari used in making the kanjeevaram saree should contain 57% silver and 0.6% gold. Tamil Nadu government has allowed this to be relaxed to 40 % silver and 0.5% gold. This GI tag protects authenticity of a kanjeevaram and maintains quality in the global market.

Changing Designs
Traditional deep colours like maroon, mustard yellow, and green are still common in Kanjivaram. But today, younger women are inclined towards pastel colors, greys, pinks, and even ivory tones. Motifs have also changed. Some weavers now include geometric patterns and birds not seen before. Some weavers even add crystals or sequins. While these changes reflect modern taste, the weaving methods remain same.

Price and Longevity
The cost of a Kanchi Pattu saree depends on the amount of Gold/Silver zari, weight of the mulberry silk, and complexity of the design. A kanjivaram silk saree can range from ₹7,000 to ₹2,00,000. But most people in India do not buy this pure silk saree just for how it looks. They buy it because it lasts. When kept well, it can remain in the family for two or even three generations.

Cultural Place
In South India, owning a Kanjivaram saree is like having a part of one's heritage. Just like the Banarasi saree in the north or Garad in Bengal. Kanjivaram saree is often part of a bride’s trousseau and is worn during major festivals. The kanjivaram sarees are not bought every season. They are gifted, kept, and remembered.
If looked after, a Kanjivaram can last longer than the person who first wore it.